Most of the focus on applying 3D printing technology to the construction industry revolves around building structures. The world’s first 3D printed office building opened this week in Dubai which has set a goal of 3D printing 25% of all buildings in the city by 2030. Taking just 17 days to print and two days to assemble, the 2,700-square-foot building was printed by WinSun Decoration Design Engineering. Back in 2014, WinSun printed 10 single-room buildings in a span of 24 hours. They followed that up last year by 3D printing a five-story apartment building and a nearly 12,000-square-foot villa.
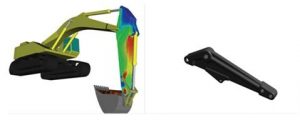
Image Credit: CCEFP
Could 3D printing be used to craft other items important to the construction industry like power tools or a bulldozer? The answer, obviously, is yes and we won’t have to wait long to see it in action.
A research team led by the Center for Compact and Efficient Fluid Power (CCEFP) is designing the world’s first 3D printed construction excavator. Printing of the fully operational steel excavator will take place at Oak Ridge National Laboratory’s Manufacturing Demonstration Facility. Teams from two of the CCEFP’s participating universities, Georgia Tech and the University of Minnesota, are designing components of the excavator. The goal is to modify and improve upon current excavator design and take advantage of the benefits that 3D printing has over traditional manufacturing.
The boom and bucket for the excavator are being designed by a team of graduate engineering students from Georgia Tech. They are working to embed the hydraulic actuators into the excavator arm. The goal is to reduce the cost of materials to manufacture these components, reduce maintenance costs and decrease the weight to improve efficiency and functionality.
Graduate engineering students at the University of Minnesota are designing the cooling system, hydraulic oil reservoir and heat exchanger. Reducing the size and weight of these systems will allow the excavator to operate more efficiently without sacrificing power and productivity.
An open competition was held for undergraduate and graduate engineering teams to design a futuristic cab with a human-machine interface for the excavator. The winners of the Additive Manufactured Excavator Design Competition will be announced next month. 3D printing of the excavator will take place in December.
The Oak Ridge National Laboratory’s Manufacturing Demonstration Facility is at the forefront of 3D printing technology. Past projects include the first 3D printed car from Local Motors using one of Cincinnati Incorporated’s Big Area Additive Manufacturing (BAAM) machine. At Maker Faire this year, they showcased a full-scale and drivable replica of a 1952 Willys Army Jeep that was 3D printed in just eight hours.
They also created AMIE, or Additive Manufacturing Integrated Energy demonstration, where they 3D printed a solar powered building and a hybrid electric vehicle that features an integrated energy system where power can flow in either direction between the house and the car using wireless technology. Architecture firm Skidmore, Owings and Merrill designed the 210-square-foot building and was assembled by Clayton Homes.
The project is being funded by a grant from the National Science Foundation (NSF). The Association of Equipment Manufacturers (AEM) and the National Fluid Power Association (NFPA) are supporting the project through industry engagement.
The final product will make its debut at the CONEXPO-CON/AGG and the International Fluid Power Exposition trade shows being held in Las Vegas in March 2017. Attendees to the show will get to see the finished excavator in action as well as a demonstration printing of a second excavator.
While none of the major manufacturers have announced plans to 3D print heavy equipment, that doesn’t mean they aren’t embracing the technology. Caterpillar has been working with various forms of additive manufacturing since 1990. They recently opened an Innovation Accelerator and an Additive Manufacturing Factory in Mossville, IL and the Cat MicroFoundry in Mapleton, IL.
Caterpillar is using 3D printing technology to produce and test prototypes, create sand molding casts and print tools and gauges used in their manufacturing plants. They are exploring ways to save time reduce manufacturing and shipping costs by 3D printing low selling parts. Caterpillar is also developing a way for dealers to print replacement parts right at the jobsite to keep their customers’ equipment up and running.
Volvo Construction Equipment has turned to 3D printing in an effort to reduce costs and cut lead time when developing new engines. VCE engineers used 3D printing to prototype and test the design of a new water pump housing for their A25G and A30G articulated haulers. They were able to shave 18 weeks off the time it would have taken to produce the prototype with traditional tooling. They also cut the production cost by 92% using 3D printing. As 3D printing technology advances to deliver items with quicker print times and in greater detail, it will be interesting to see how other manufacturers incorporate the technology.
2017 is going to be an exciting year for 3D printing applications in the AEC industry. In addition to the excavator, we will also get to see the first 3D printed bridge. MX3D, an R&D company in the Netherlands, is working to 3D print a 24-foot long pedestrian bridge over a canal in Amsterdam in next year.
Starting on opposite banks, at least two 6-axis industrial robots will begin printing the bridge using an additive printing technology similar to welding. A new steel composite developed at Delft University of Technology to print the bridge by adding layer after layer of molten steel on top of each other to form the structure. As the structure is being printed, the robots will travel across the printed portions, eventually meeting in the middle upon completion.