Worker safety should always be the number one priority of every construction company. Safety meetings and toolbox talks should be conducted on a regular basis to educate workers on safe work practices and stay compliant with regulations regarding safety and training.
Safety meetings and toolbox talks are important to building a strong safety culture and reinforcing your company’s commitment to protecting your workers. Holding regular safety meetings and toolbox talks can prevent workers from getting complacent and avoid taking safety for granted.
These meetings and talks are also the perfect time to introduce new safety policies and procedures you are implementing as well as to provide training on new safety rules and regulations in order to stay compliant with state and federal OSHA standards.
Project Kickoff Safety Meeting
Before you start work on a new project, hold a safety meeting with all employees who will be setting foot on the jobsite. Kickoff meetings should be structured to cover the risks and workplace hazards that will be present throughout each stage of construction.
Safety topics covered in a kickoff meeting should include safe work practices for the various activities and tasks being performed, the selection and proper use of personal protective equipment (PPE), and basic first aid practices. Discuss the engineering safety measures that will be in place on the jobsite.
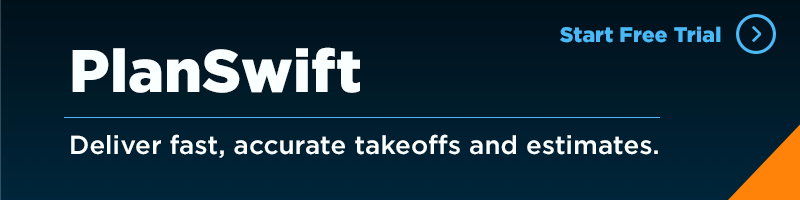
A visit to the jobsite should be scheduled to let workers familiarize themselves with the layout and location of the project. Make sure to point out the location of the jobsite trailer or office, where materials, tools, and PPE are being stored, the location of first aid kits, and directions to the nearest hospital.
Make sure workers know who the safety manager or supervisor they should report to if an accident occurs or if they witness unsafe work practices. Inform employees that they have the power to stop work to correct unsafe work acts or conditions.
Toolbox Talks
Once the project is underway, conduct toolbox talks on a daily or weekly basis to reinforce your focus on safety. Toolbox talks, sometimes referred to as tailgate meetings or safety briefings, are short, informal safety meetings held at the start of each day or shift.
Toolbox talks are a great way to reinforce safety basics, focus on high-risk scenarios and to inform workers about changes to the jobsite and working conditions that may have occurred since their last shift. Be sure to discuss cover any accidents or injuries that have occurred and how they could have been prevented.
Toolbox talks can be broken out into smaller groups to focus on individual trades or work activities for certain individuals. Don’t hold a toolbox talk on electrical safety if sitework and excavation is the only thing being done that day.
Inclement weather like heavy wind, snow, ice, and rain can create unsafe conditions. Use toolbox talks to remind workers to be extra cautious when additional jobsite hazards from the weather are present or expected.
Use site inspections as teaching moments when unsafe work actions or conditions are observed. If you notice workers walking around without hard hats on one day, focus your next toolbox talk on the proper selection and use of PPE.
Be sure to focus on the positive, too. Toolbox talks should highlight safe working practices observed to provide positive reinforcement and applaud workers who are adhering to safety rules and regulations.
Toolbox talks are a great time to have employees inspect the equipment, tools, and PPE they will be working with that day to ensure they are in proper working condition.
6 Keys to a Successful Toolbox Talk
- Keep it short. Toolbox talks should be around 5 – 10 minutes.
- Focus on one topic relevant to the work being done that day.
- Get workers involved by asking questions or having them demonstrate safe work practices.
- Be sure to cover changes to the site or working conditions.
- Have employees inspect tools, equipment, and PPE.
- Allow for questions and answers at the end of the toolbox talk.
The internet is a great resource if you are looking for ideas or topics for your next toolbox talk. Sites like CPWR, oshatraining.com, and Safety Toolbox Topics offer free topics and discussions for your next toolbox talk.
Safety Training
All new employees, regardless of their work experience, should be trained on safe work practices, PPE requirements and adherence to safety regulations. Formal safety training should be structured into digestible blocks of information to build on the lessons previously taught.
Employees should be able to recognize workplace hazards and unsafe working conditions. Evaluate your employees’ safety knowledge with tests and quizzes to ensure that the training they have been provided is understood and they have retained the knowledge they have learned.
Safety training shouldn’t be limited to new employees. Refresher courses and ongoing training helps keep safety a top-of-mind priority for your employees and reinforces your company’s commitment to safety.
Corrective measures such as retraining should be part of any disciplinary action when an employee is found to be working unsafely or disregarding safety requirements. It’s always a good idea to do a little research before handing down punishment. Determine if the behavior was a blatant disregard for the safety rules or whether it was a result of inadequate safety training.
Regularly evaluate and make adjustments to your training as needed to ensure you are providing your employees with the knowledge to keep them safe on the jobsite and reinforce your safety culture.
Need more project leads? ConstructConnect finds you the best construction projects to bid on and win more work.
