Arguably one of the most essential documents to ensure a construction project’s success, a material takeoff (MTO) is a comprehensive list of all materials and their quantities required to complete a project derived from the construction drawings and plans. Also referred to as a construction takeoff, quantity takeoff, or simply a takeoff, is a crucial element in accurately estimating and bidding on a construction job.
Creating your material takeoff requires measuring, or taking off, the various components of a construction project in order to calculate how much material is needed for each.
For example, if you’re a drywall contractor, you’ll measure the linear feet of all the walls and the height of the walls to calculate the square footage of the walls. Using those measurements, you would then calculate all the materials (drywall panels, tape, mud, screws, etc.) and quantities of each needed to install the walls. If you’re also doing the ceilings on the project, you would measure the square footage of the ceilings and calculate the materials and quantities needed to install the ceilings.
Why Material Takeoff Is So Important
Measuring and calculating material takeoffs are a vital part of any construction project. The person or team preparing an estimate relies on the information provided to determine the total cost for materials as well as the labor, equipment, and other associated costs. With the ability to completely dislodge a project’s budget, workflow, or even completion, material takeoffs are vital for all parties involved to initiate and oversee a project from inception to completion.
Your bids are only as good as your estimates, and your estimates are only as good as your takeoffs. If the initial takeoff measurements, the specific type of materials needed, and the calculated quantities of each are off in any capacity, it could negatively impact the project and its budget.
Let’s Breakdown a Material Takeoff
We know that a material takeoff is a comprehensive list of all materials required to complete a project correctly. While a material takeoff does include all raw and prefabricated items that will be used in construction, it does not include the actual cost of those materials, the equipment and/or tools, or the labor needed to complete the project.
That is what differentiates the takeoff from the estimate, as it solely covers the materials and the quantities needed of each to complete a project. Those material quantities are used during the estimating process to determine your material costs as well as your additional costs for labor, equipment, overhead, etc.
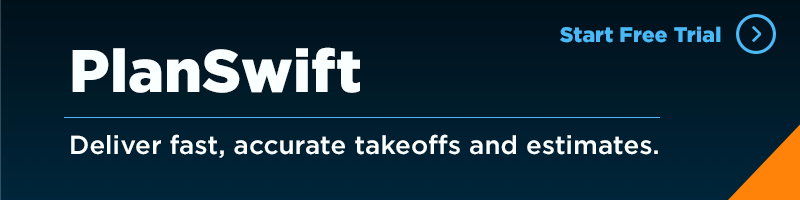
A material takeoff starts with your construction drawings, plans, and project documents. From these documents, you may quantify various building objects:
Count: For individual items like sink faucets, light fixtures, and doorknobs, the material quantity takeoff specifies how many of each are needed.
Length: Along with the basic dimensions, the material takeoff provides the length for items such as pipes and cables (as well as the quantity of each).
Area: The material takeoff for an area is typically measured in square feet. The surface area is commonly used for walls, ceilings, floors, and roofs for materials like drywall, paint, flooring, etc.
Volume: For projects like a parking lot, the volume of asphalt per yard is critical information needed for the material takeoff.
Manual Versus Digital Takeoff
For years the only option for delivering material takeoffs was by doing them manually—meaning that the general contractor or estimator had to measure and count all the components using paper and pencil from the plans or blueprints. They would then have to perform various calculations to determine the material quantities needed for each project. Once the material takeoff was complete, more calculations would be needed to accurately estimate the project.
Manual takeoffs are prone to a number of errors, from inaccurate measurements to miscalculating material quantities to just missing items, either during measurements or when calculating quantities. Paper blueprints can be expensive to produce and can also cause issues regarding the ever-changing nature of projects and their demands. This is where the incredible power of digital takeoff makes its grand entrance.
Digital takeoff and estimating software have made the material takeoff process extremely efficient and accurate. Digital takeoff software not only achieves the obvious perk of saving hours of time completing meticulous tasks but also allows for better collaboration, reduces errors, and allows estimators to bid on more projects.
The Digital Takeoff Process
Although the workflow of a digital material takeoff varies depending on the software you are using, the type of project, and other related factors, the MTO begins its course by uploading digital plans and documents that can then be used to start performing takeoff. After uploading the plans and setting up the projects, the user can then set the scale on the plan sheet and start using the tools to start measuring and performing takeoff on the screen. The measurements are saved, and your material quantities are calculated.
Digital Takeoff & Estimation Solutions
Mistakes in takeoff and estimating can quite literally break the bank. Using a digital takeoff solution helps estimators avoid mistakes in delivering accurate material takeoffs to precisely estimate and bid projects.
The market is full of digital takeoff solutions to choose from. ConstructConnect offers takeoff and estimating tools to meet the needs of any type of contractor or project. If you already have experience doing takeoffs manually, the learning curve to get up and running is relatively small since the software can be adapted to your current takeoff process and workflow.
On-Screen Takeoff
On-Screen Takeoff is a robust takeoff solution that, provides tools for quantifying medium to very large construction projects. On-Screen Takeoff can be used in conjunction with Quick Bid to create detailed material takeoffs, construction estimates, total job costs, and formal proposals for bidding.
Takeoff Boost™ is the new artificial intelligence-based add-on feature for On-Screen Takeoff that automatically performs takeoff measurements for area (footprint, gross area, net area), linear (walls/boundaries), and counts (toilets, sinks, bathtubs, single swing doors, double swing doors, sliding doors, parking spaces) to deliver takeoff measurements up to 15x faster than using OST alone.
PlanSwift
PlanSwift is a takeoff and estimating solution used by general contractors and trade contractors to perform Material Takeoff and create a construction Estimate in a fraction of the time it takes to perform these tasks manually. Trade specific to accommodate many construction estimating needs. Drag and drop material and labor assemblies into a material takeoff, then export or print to share.
QuoteSoft
QuoteSoft brings digital takeoff to the mechanical, piping, plumbing, HVAC, and ductwork trades. Powerful tools and parts catalogs allow an estimator to create comprehensive material takeoffs and labor estimates quickly and with greater accuracy than ever.
Final Thoughts on Material Takeoff
Material takeoff quantities are an important part of any construction estimate or bid. They inform not only how much materials you will need to complete a job, but also impact your labor costs, equipment costs, and project timeline. Ensuring your materials takeoffs are accurate allows your estimates to be more precise and, in turn, for your bids to accurately reflect your job costs. This allows you to bid more competitively and win more jobs.