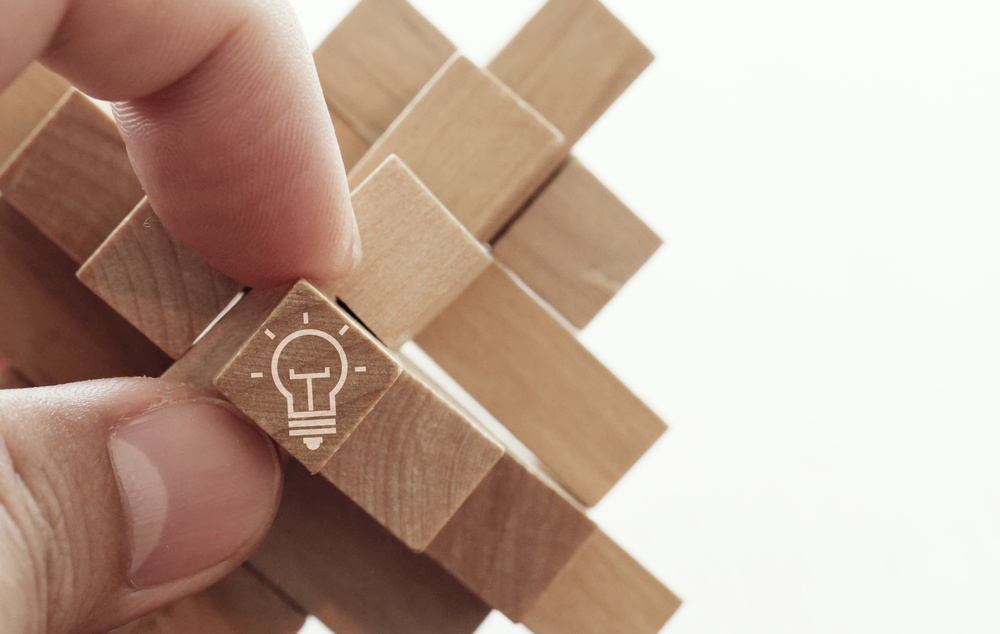
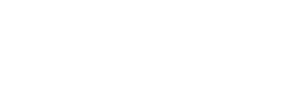
Given projections for a dramatic shortage of construction labor due to retirement and recent policy changes related to immigration in Canada and the United States, the future of any continued growth of housing and commercial projects could lie in the hands of modular processes.
Modular has collateral benefits that could also improve profits. For example, since time is money and modular construction requires less labor, there could be more efficiency and reduced overall costs.
The case for modular construction in the U.S. is clear, write Jose Luis Blanco, Dave Dauphinais, Garo Hovnanian and Rob Palter of McKinsey Global.
“Manufacturing building components in factories and assembling them onsite offers solutions to many of the construction industry’s challenges, which include high material prices, disrupted supply chains, and shortages of skilled labor.”
However, they see modular construction companies presenting themselves to potential customers largely as design and technology companies, with websites set against a background of computer screens and computer-aided design (CAD) renderings.
“Yet modular construction is still construction,” they write. “Every modular building system needs a developer willing to buy it, a design able to accommodate it, a bank ready to finance it, and a skilled onsite team ready to install it.”
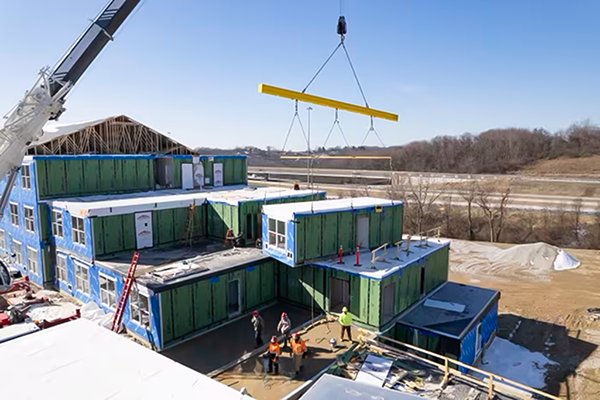
Assembly was underway last year on Greystar’s six-building, a 312-unit apartment complex near Pittsburgh. Image: Greystar
Several experts attending Bisnow’s Los Angeles Prefabrication, Modular, and Mass Timber event last August expressed the need to appreciate the modular process at all project levels.
“People don’t realize that off-site construction is not about less due diligence,” said Assemblage Works CEO Michael Mathews. “The reality is it’s actually four times the amount of due diligence.”
Of the developers who have recently invested in modular construction, no firm has embraced the trend as warmly as Greystar Real Estate Partners. It is the largest manager and developer of apartments in the U.S., with nearly 900,000 multifamily units and student beds under management globally.
In April 2023, Greystar launched its own modular construction business, Modern Living Solutions (MLS), which combined development, construction, and modular manufacturing under one roof.
By December 2024, MLS had already completed its first project, a 312-unit modular apartment complex called Findlay, 16 miles outside of Pittsburgh.
Findlay comprises one-, two-, and three-bedroom units ranging in size from 662 to 1,373 square feet. The six buildings are laid out in a garden-style setting. The project was completed 40 percent faster and at a cost 10 percent lower than traditional construction methods, with 90 percent less waste.
Other major developers like Greystar are beginning to explore modular processes as well.
Related California, an affiliate of New York-based Related Companies, has completed the first phase of the 10-acre Sugar Pine Village, the largest residential development to be approved in South Lake Tahoe. Some of the later phases will utilize modular construction due to its suitability for Tahoe’s short building season.
Meanwhile, innovation in volumetric construction around the world continues to expand its versatility and potential.
At Graz University of Technology in Austria, a new timber module system has been developed that would allow easy removal and replacement of individual volumetric apartment units. The system combines the advantages of modular wood construction with the advantages of skeleton construction.
The skeletal frame acts as a supporting structure for flexible floor plans. These can be adapted by inserting or removing partition walls as occupant requirements change over time, thereby future-proofing the building. Currently, the skeletal system allows for a six-story all-timber building or up to 24 stories if a concrete core is used.
As promising as modular construction may be, Blanco, Dauphinais, Hovnanian, and Palter of McKinsey Global write, “The challenge arises at the interfaces between modular companies and the wider construction ecosystem.”
Ultimately, demographic and economic pressures will force financiers, designers, modular factory operators and builders to come together.
“Overcoming these challenges could unlock a new phase of accelerated growth.”